A Winning HazCom Gameplan
- Safety Experts
- Aug 2, 2023
- 4 min read
Missing or inadequate hazard communication programs were OSHA’s no. 1 cited issue in 2022 in the general industry sector. There were a total of 2,424 cited violations, which moved it up from the number two spot the previous year when it was second only to respiratory protection.
Chemical manufacturers and importers are required to classify the hazards of chemicals they produce or import, and all employers are required to provide information to their employees about the hazardous chemicals to which they are exposed. OSHA requires this to be done through a written hazard communication (HazCom) program, labels, other forms of warning, safety data sheets, and training.
It’s common to associate hazardous chemicals with images of barrels of toxic liquids and large pools of waste. But in reality, even common substances like paints, cleaners, degreasers, or detergents in the workplace may be considered hazardous chemicals. Without an effective hazard communication program, you could be putting workers at risk and face financial penalties.
An effective HazCom program ensures all hazardous chemicals in the facility are identified and labeled, and that up-to-date, properly written safety data sheets are available. It also includes provisions for training all potentially exposed employees on chemical hazards, safe handling, and protective measures. Below are five key steps to ensuring your HazCom program is successful.
1. Document Inventory and Exposure
HazCom programs start with inventorying and classifying any hazardous chemicals a facility produces, imports, handles, or creates through the mixing of different substances.
This can be a significant undertaking for larger facilities, but the program’s effectiveness will depend on the accuracy of your hazardous chemical inventory, and your facility must have this list present and accessible to employees and auditors.
Before you begin the documenting process, consider reading 29 CFR 1910.1200(b)(5 & 6) so you’ll know what the exceptions are for certain chemicals.
Another critical component of the plan is developing an equally thorough list of the positions and people who will handle these hazardous materials. Any employee who could be exposed during normal operations or in an emergency needs to be properly documented. This process will tie directly into effective training programs.
2. Label Materials
OSHA has specific marking and labeling requirements for different types of containers. Employers should know these requirements in detail and ensure that containers are marked appropriately in accordance with 1910.1200.
Typical methods include stickers, signs, and placards. When it is impractical to use these, for example, when harsh conditions exist, or there’s a need to protect trade secrets, process sheets, batch tickets, operating procedures, or other written materials can be used to communicate chemical hazards to personnel. OSHA requires this information to be in English. You can add the information in other languages to the material, as long as the information is presented in English as well.
3. Obtain and Maintain Safety Data Sheets
Any company producing or importing chemicals will be responsible for classifying the hazards of the chemicals. Other employers that have potential exposure still need to maintain a safety data sheet for each hazardous chemical they use, with some exceptions referenced in Step 1.
If the chemical supplier did not provide a safety data sheet, it’s up to the employer to obtain or create one. Covering all 16 sections in these documents is an intensive process. The full list of what needs to be covered can be read here.
4. Implement Training Programs
After identifying hazards and determining workers who could be exposed, you’ll need to train employees to be aware of the information they need. This training should include topics such as location and use of safety data sheets, locations and operations where chemicals are present, the contents and functioning of the program, lists of chemicals, protective measures, and other information specified in the HazCom standard.
Employees should be trained immediately after they are assigned, and whenever a new chemical hazard is introduced into their work area. For example, training should be updated and delivered when a new product or process is introduced that alters the hazardous chemical landscape of the company’s operation. That also means it’s time to update safety data sheets. Employers should also consider how often they want to conduct important refresher training.
5. Maintain Records for Audits
In addition to an overarching concern for the health and safety of your employees, safety data sheets and training records should be continuously updated and readily available for OSHA inspectors.
OSHA typically doesn’t conduct routine audits except for some specific industries. They will inspect targeted facilities, for example in the event of fatalities, severe injuries, or worker complaints.
Penalties from these inspections differ based on the nature and severity of violations. The penalty for a single first-time serious violation can exceed $15,000. If the violation is repeated or OSHA determines it is willful, the penalty can surpass $156,000.
An effective HazCom program is critical to ensuring employee safety, which should be the number one priority of any manufacturing company. By following these five key steps, you can implement a successful HazCom plan that keeps workers safe while improving efficiency by preventing costly and time-consuming OSHA audits and shut-downs due to unnecessary chemical contamination.
Source: https://rb.gy/y0bdm
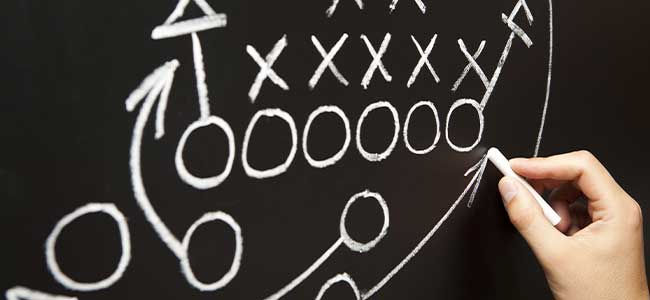
Comments