Building a Culture of Safety: Strategies
- Safety Experts
- Jul 9, 2023
- 4 min read
Year after year, occupations in the construction industry remain the most hazardous to workers. Since 2008, no industry's registered a higher on-the-job death toll. On top of that, the construction industry also has the second-highest worker suicide rate, reflecting the crushing stress that often comes with its jobs.
That reality means construction firms and project owners have both a financial—and moral—obligation to do everything in their power to build a culture of safety that mitigates the dangers inherent to their work. The good news is that there are a variety of ways to accomplish that and plenty of research to demonstrate the need to put them into practice.
To elaborate, here are the four core tenets of a solid construction firm safety culture and how to apply them to build that culture from the ground up.
1. Make Productivity Subordinate to Safety
One of the most important keys to establishing a safety culture within a construction firm is to make productivity subordinate to safety. This is critical as it sends an unmistakable message that nothing—even the almighty dollar—is more important than the safety and well-being of employees both on and off the job site. It's a necessary and vital step to combat the pervasive perception among workers that the opposite is true. Just how pervasive is this perception?
According to a survey conducted by the National Safety Council, one in three American workers believe their employer prioritizes productivity over safety. Importantly, 60 percent of that survey's respondents worked in the construction industry, lending even more relevance to the statistic. It's a clear sign that construction firms still have a long way to go on this score.
To change your employees' minds, one idea is to start by weighing existing key performance indicators against safety performance—in other words, rewarding employees and managers who sustain high productivity safely while admonishing those that don't—even if their overall productivity levels exceed their safer counterparts. Doing that should break the "productivity at all costs" mentality that dominates many construction sites and projects.
2. Create Mitigation Processes for Common Safety Concerns
The next core tenet of a solid construction safety culture is to create effective mitigation processes for common safety concerns. In other words, you need to identify the specific safety issues inherent to the work you're doing and establish clear, visible processes to deal with them.
For example, it's widely known that 60 percent of all construction fatalities stem from electrocution, falls, getting struck by falling objects, and crushing or pinning injuries. Therefore, beginning by establishing processes to prevent such injuries is a great place to start. For example, there are multiple measures you could implement to prevent falls, such as:
Conducting fall risk assessments
Supplying the latest safety equipment
Staging surprise best-practices inspections
Offering regular employee training
Offering incentives for at-risk employees that adhere to safety standards
By creating individual mitigation processes for each applicable safety issue, you can embed a safety mentality at all levels of your company that's highly specific to the work you do. Plus, the processes provide a ready roadmap to ramp up safety improvement efforts whenever necessary.
3. Enforce Safety Accountability at All Times
Another core tenet of building a safety culture for your construction firm is one that some managers may be loath to put into practice—a zero-tolerance safety accountability standard. It means letting every employee know that unsafe behavior is unacceptable, even if the employee only puts themselves at risk through their actions. The bottom line is that every worker must know that their job's contingent on their willingness to observe all safety regulations and procedures at all times.
This is often a difficult thing to do, owing to the extreme labor shortages now faced by construction companies all over the country. However, in the long run, an employee who refuses to observe safety regulations and procedures may not be worth employing. In the end, they could cause injuries to other employees and further exacerbate labor issues—not to mention liability for the company.
4. Invest in the Latest Safety Equipment
Lastly, construction companies wishing to establish and build a safety culture have to put their money where their mouth is and invest in the latest safety equipment for workers. Nothing tells your employees that you take safety seriously more than equipping them with everything they need to stay safe.
For example, you could invest in one of the many high-quality construction safety apps now on the market. They make it easy for your employees to manage safety compliance and report safety issues in real-time so you can address them immediately. Or, you could begin using drones and robotics to handle work that would otherwise require putting an employee in harm's way.
Common examples of this are site surveying from altitude or examining under-construction areas that contain ongoing hazards. Every dollar you spend on technology that prevents a worker from undue risk is a dollar well-spent and a building block in your new safety culture.
A Safety Culture From the Ground Up
The preceding safety culture tenets will simultaneously improve your construction firm's safety performance while placing safety front and center in the mind of every employee. Over time, that will encourage a safety-first mentality throughout your organization. It will also help you establish safety procedures that remain both effective and self-reinforcing for the long term. At the end of the day, that's what a safety culture is made of—and instilling it in your firm will become a self-fulfilling prophecy.
Source: https://rb.gy/mdg1i
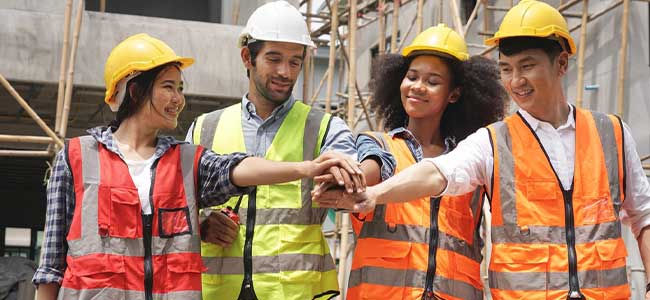
Comments